Omnia’s BME launches its most advanced electronic blast detonation system
Safe and efficient blasting has taken a momentous step forward with Omnia Group company BME’s launch of AXXIS Titanium™, one of the world’s most advanced electronic blast detonation systems.
BME Managing Director of the SADC region Ralf Hennecke has hailed AXXIS Titanium™ as a significant advance for the company’s ever-evolving technology offering, securing BME’s position among the global leaders in electronic delay detonator (EDD) design.
“Our release of AXXIS Titanium™ raises the bar globally for the electronic detonator market,” said Hennecke. “This flagship product reflects our continued focus on digital advancement on mines, and is designed to seamlessly integrate with BME’s software systems and hand-held digital tools.”
AXXIS Titanium™ improves safety levels and manufacturing quality through enhanced communication with the detonator during manufacturing to avoid defects. Performance is raised through the increased blast duration per detonator, more units per blasting box and precise firing accuracy.
“Most importantly, the AXXIS Titanium™ system was built for the blaster and blast engineers who work with the product every day,” he said. “The robustness of the wire, the easy-to-use interface and the improved integration will improve efficiency in terms of time, data and reporting.”
As the latest generation of BME’s popular and well-proven AXXIS™ system, AXXIS Titanium™ takes blasting safety and flexibility to a new level, according to Tinus Brits, BME’s Global Product Manager for AXXIS™. BME has over the decades made regular advances in the performance, safety and reliability of this innovative solution, said Brits.
“This latest iteration builds on the achievements of the AXXIS GII™ model and raises the bar in many of the features that have served our customers so well,” he said. “These include further refinements in safety, accuracy, flexibility, ease of use and speed in preparing each blast.”
Safety remains the watchword, with the incorporation of a Swiss-designed application-specific integrated circuit (ASIC) chip in the BME detonators, delivering several added benefits. The ASIC gives the system more internal safety gates against stray current and lightning, enhancing safety levels and allowing for inherently safe logging and testing.
Dual safety
“A unique innovation is our use of dual capacitors and dual voltage, allowing us to conduct low voltage logging to avoid any chance of detonation,” he said. Blasts are initiated by a robust, encrypted blast command ensuring that detonators all receive their respective commands and fire as planned. He emphasised that the detonator will only react if it receives the correct, encrypted firing sequence from the blasting equipment, not from any other source.
“We have developed AXXIS Titanium™ to be resistant to electro-magnetic pulses (EMPs) caused by the blast, which can affect the accuracy of detonators or even cause them to fail,” he said. “Our intensive tests in conjunction with the Council for Scientific and Industrial Research (CSIR) showed that our detonators can withstand a significant EMP without any impact on their timing.”
He noted that underground blasting – within confined spaces – made detonators particularly susceptible to re-setting and misfiring due to voltages from EMP, as well as from dynamic pressures. Over-moulding of all components on the electronic board protects the detonators against dynamic pressures, and isolates components from any induced ground currents – such as electrostatic discharge and lightning strikes.
Easier timing, more dets
The ASIC chip boasts more memory and processing speed, facilitating easier timing and centralised programming if the timing needs to be changed after being conducted on the bench. It also achieves lower power consumption with the incorporation of dual capacitors – so more detonators can be initiated per blast. The system can now manage 1,000 detonators per blasting box, doubling the capability of the previous generation.
Brits also noted that up to 20 blasting boxes can be linked and synchronised through hard wiring, enabling the possibility of initiating up to 20,000 electronic detonators in a single blast – doubling the capacity of the AXXIS GII™ generation.
“AXXIS™ has been proven in some of the largest mining blasts on record, giving mines the opportunity to conduct fewer blasts – thereby reducing downtime due to pit closures,” he said. “The ultra-low energy micro-chip is also less susceptible to leakage and cable resistance and extends the firing time to a maximum of 35 seconds.”
Speed, testability
The ease of use and on-bench logging is among the key benefits of AXXIS Titanium™. Hennie du Preez, BME’s Manager AXXIS™ Support, highlighted the one-step logging and testing of detonators, as well as the simple fault-finding and quick corrections on the blast pattern.
“Everything is built into the logger, which can now do the programming, scanning and testing,” said du Preez. “The market appreciates the speed at which you can now fire a blast; after the detonators have been programmed, you can start up the controller from the view site and blast within two minutes.”
The speed of the ASIC chip on the system’s board cuts the programming time by half, he noted.
Blasting for sustainability
The accuracy of the detonation delays has been further fine-tuned, reaching a 0,02% firing accuracy for consistent and quality blasting that results in better rock fragmentation and consistency. He highlighted the positive impact this has on the efficiency of key mine measurables like loading rates and crusher throughput. This in turn helps mines improve their carbon footprints as they pursue increasingly vital sustainability targets. In this way, BME’s technology innovation is closely aligned with the Omnia Group’s ongoing focus on sustainability, which prioritises zero harm and positive impact to build a better future.
Accurate blast design and initiation also allows mines to ensure they are operating within regulatory limits regarding vibration control.
“Commands from the operator are written into the detonator’s non-volatile memory, so that it cannot be over-written or deleted,” he said. “This is very useful for post-blast analysis if required, even the blast command is recorded by the memory chip.”
Integration
He highlights the value of technological integration of AXXIS™ with BME’s other innovative solutions such as its BLASTMAP™ blast planning software, XPLOLOG™ platform and cloud-based storage for post-blast analysis. The system also integrates with third-party blasting software.
“The AXXIS Titanium™ system supports BME’s data integration vision for customers,” he said. “This aims at giving customers better control of the entire blasting process, as well as customised reports and data solutions to optimise efficiency and cost.”
Roll out
The commercialisation of AXXIS Titanium™ follows extensive laboratory and field testing in South Africa, leading to the recent award of an Inspection Authority certificate by the Department of Mineral Resources and Energy. Enthusiastic uptake of AXXIS Titanium™ has already begun in BME’s southern African market, and the system will soon be rolled out across BME’s extensive Africa footprint.
Further afield, Australia is also an important market for this AXXIS™ upgrade, especially due to the complexity of their coal seams and methods – such as through-seam blasting, said Du Preez.
“With multiple seams requiring the loading of detonators to prevent contamination of coal with waste, longer firing delays are an important benefit,” he said.
The system is already certified in Australia, Asia Pacific and the United States, and the necessary regulatory processes are underway to certify AXXIS Titanium™ in Canada and the rest of the company’s global territories.
Training
Providing the necessary training for customers to use the new system remains an important part of BME’s contribution, according to Tom Dermody, technical services manager at BME Australia-Asia. Dermody noted that the training has evolved over the years as mines have become more familiar with electronic detonation technology, and more recently as the Covid-19 pandemic has restricted access to mine sites.
“We now split the training between virtual sessions online and practical sessions on the bench,” he said. “As electronic initiation systems are used more widely, the training tends to focus more on BME’s specific offering. Mines’ blasting teams can now do most of the introductory training online, which we then augment with a more hands-on training element on-site which focuses on practicalities.”
AXXIS Silver™
For customers in smaller mining operations, quarries, construction and demolition, there is also a slimmed-down version of this system in the form of AXXIS Silver™ – for applications that do not require such large blast capability. Du Preez emphasised, however, that AXXIS Silver™ has the same microchip, safety features and ease of use as AXXIS Titanium™. It will shortly complete the required testing protocols to achieve the necessary certification.
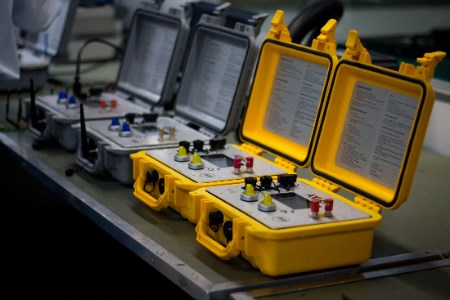
About BME
As a member of the listed, diversified chemicals group Omnia, BME is a mid-tier, integrated partner in the global blasting and explosives industry. Our innovative range of fit-for-purpose technology, products, services and software solutions are underpinned by our depth of expertise in the field.
Since our formation in South Africa over three decades ago, our global footprint has expanded to serve customers in Australia, south-east Asia, the Americas and 17 African countries including South Africa, Namibia, Botswana, Zimbabwe, Zambia, Swaziland, Angola, Malawi, Mozambique, DRC, Sierra Leone, Mali, Burkina Faso, Mauritania, Ivory Coast and Eritrea.
Our experience of working in Africa, often in remote and difficult locations, allows us to provide a flexible and seamless service, and to supply and commission emulsion plants at any location. With a network of manufacturing and product development facilities, our focus is on providing security of supply – supported by the latest technology for optimal blast quality.
Our agile operating model allows us to cater to the full spectrum of mining requirements in both surface and underground environments. In line with the broader Omnia Group strategy, we form strategic partnerships around the world to ensure that our solutions are localised and customised.
We take a holistic and solutions-based approach to our projects, collaborating closely with customers and third party business partners to achieve operational excellence. We nurture a culture of ‘Safety for Life’ across our business, prioritising ESG and work towards a reduced carbon footprint. In the communities we operate in, we aim to sustain livelihoods and leave a better world.
The supply security that we assure to customers is based on our collective Omnia Group manufacturing capability and collaboration, including two modern nitric acid plants, a nitro- phosphate plant, an ammonium nitrate facility, two central emulsion plants and two automated AXXIS™ electronic detonator plants. We also operate a cartridge explosive facility, a non-electrics assembly plant, a manufacturing and assembly facility for our mobile manufacturing units (MMU), and remote emulsion plants.
Our technology offering is cutting-edge, allowing us to provide a wide range of technical services from routine blast monitoring to advanced online technical consultancy and optimisation projects. We leverage our Blast Alliance™ integrated software portfolio to support customers in their digital transformation journey toward smart mining.
We continuously improve our equipment and digital solutions to optimise productivity and efficiency at mining operations. Among the key outcomes we pursue with customers are reduced ore dilution and finer fragmentation for increased mineral recovery and higher plant throughput rates.
With our depth of expertise and innovative technology, we can offer customers a range of specialised services – from blast planning and down-the-hole full blasting services, to blast consulting, auditing and monitoring.
Hi dear manager, let me introduce myself my self, I’m name is Nicholas underground production and development shift boss, production charge up trainer with more experience in electronic detonator system blasting remote.
In:logging electronic detonators ikon II& III in logger.
In:fixing leakages and errors during logging.
In:using blater 2400 and 3000 able to install more blaster from different levels the underground to a remote box to surface and blast the stope from the surface.
I can be useful for you. For more informations inbox