Five Things You Didn’t Know About Drilling
Drilling is the process of creating a hole in a hard surface, specifically where the length of the hole is greater than its diameter. It’s an integral part of the mining process, albeit less dramatic than, say, blasting. If you’re curious to know why mining couldn’t exist without this essential process, read on to discover five things that you may not know about drilling.
- Drilling is central to mineral exploration
Every single mining project begins with exploration. This is the first stage, before any mining occurs, in which geologists and various other experts are brought in to identify “prospects” – that is, locations where significant concentrations of minerals have accumulated over many thousands of years. This step in the mining activity process is often referred to as “prospecting” or “surveying”.
Once a particular prospect has been identified, further exploration is required to determine some of the important characteristics of a mineral deposit, such as quality and quantity – and that’s where drilling comes in.
The ground is drilled to collect “core samples”: cylinder-shaped sections of rock that are extracted using what’s known as a core drill. These core samples are then placed in special boxes in the order in which they were extracted, so that geologists can conduct more detailed analyses to ascertain the types of mineral present, the different structural features, and the strength of the material.
While each core sample is usually only 55 millimeters or so in diameter, the core holes from which they are extracted can measure hundreds or even thousands of metres in length. Depending on the results of the exploration work, a decision will then be made as to whether the site is a viable location for a mine. If it is, the process of obtaining the millions of dollars of investment that is required to develop a mine can begin.
- Diamonds come full circle when drilling in search of minerals
Diamonds, one of the hardest naturally-occurring materials on earth, play an important role in exploration drilling. These precious stones are the key component of a core drill, where they are sprinkled throughout the drill bit. As the drill bit wears down, more diamonds are exposed, allowing the drill to continue cutting its way through the rock. Although these diamond core drills are not actually used to drill for diamonds, there is still a certain symbiosis to the fact that, after being mined, the stones are most likely to be utilized in the mining industry itself – when they aren’t being made into jewellery, that is.
The diamond core drill was invented by the French engineer Rodolphe Leschot, who patented the device in the United States in 1863. Its first practical use was drilling the blast holes used in the creation of the Fréjus Tunnel through Mont Cenis on the French-Italian border.
- Two types of blasthole drilling rigs dominate in the mining world
While diamond drills are typically used for collecting core samples, the blasting process (in which explosives are loaded into purpose-drilled holes) relies on blasthole drilling, and one of two basic methods: percussion and rotary drilling. Percussive drills chip away at rock by raising and dropping a large hammer bit into a hole and are known, quite descriptively, as ‘down-the-hole hammer drills’.
Rotary drills – as their name suggests – work by rotating, allowing the sharp drill bit to cut into the rock. The grooves on the drill bit are designed to retrieve the separated sediment and rock from the hole, as the drill rotates. For extremely hard surfaces, a combined rotary-percussive drill is often used, which employs both actions.
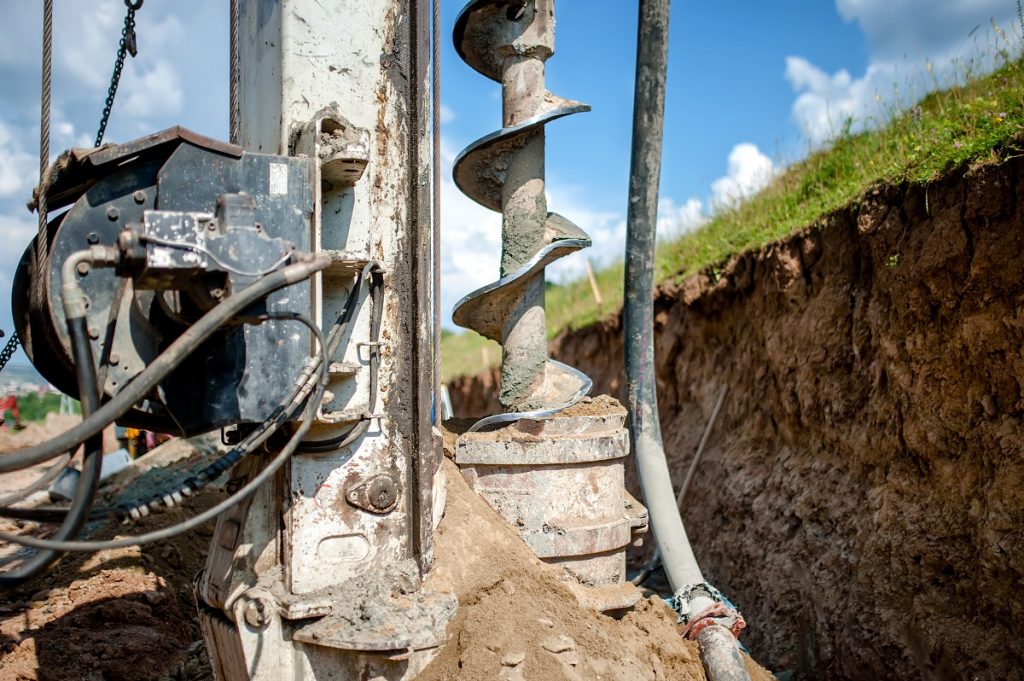
- Autonomous technology is revolutionising drilling
Autonomous drilling technology is a game-changer for the drilling process, making it safer, more accurate, and consistent. In Pilbara, Western Australia, Rio Tinto has been using an Autonomous Drill System (ADS) in its iron ore operations since 2008 and, as of August 2018, the company’s ADS-enabled equipment had drilled more than 5,000 kilometres through the earth.
The technology allows a single drill operator to control multiple drilling rigs simultaneously from a remote location – even if the rigs weren’t all made by the same manufacturer. This enables the operator to work away from the dust, noise, and vibrations that come with the territory. In fact, Rio Tinto’s autonomous drills are operated from the company’s operations centre in Perth, more than 1,500 kilometres away.
But autonomous drilling isn’t just safer. The technology also enables each individual machine to operate at maximum efficiency, drilling more metres per hour than would otherwise be possible. An impressive capacity for data collection is another advantage. Analysing data from each autonomous drill gives mining companies access to valuable insights which can help to evaluate the ecological impact of their drilling operations.
- Exploration drilling is identifying new mining opportunities in Zambia
Even though exploration activity in Zambia has dwindled significantly in the last decade – with a lack of long-term policy stability making outside investors far more circumspect about parting with the capital necessary to fund exploration projects – there are currently a handful of prospects in the pipeline. Some of these prospects have the potential to be converted into new mines – provided the investment environment is attractive enough.
“Autonomous drilling isn’t just safer. The technology also enables each individual machine to operate at maximum efficiency, drilling more metres per hour. ”
Two such prospects are the Zamsort and Zaco copper projects in North-Western Province, in which Arc Minerals has a respective 66% and 72.5% shareholding. Once Arc Minerals had acquired interests in these exploration licenses, the company conducted a comprehensive airborne geophysical survey of the prospects in 2018. This non-invasive technique measures the earth’s magnetic field, naturally-occurring gamma radiation from bedrock and soils, as well as electrical conductivity in the ground to allow the geology of an area to be mapped. Upon completion of the airborne geophysical survey, twelve target areas were identified.
In mid-2019, a local drilling contractor was brought in to further test the identified prospects using diamond drilling rigs, and an initial 7,500 metre drilling programme commenced. The results of these drilling operations were revealed in February 2020, and showed that at least two of the prospects had the potential to develop into significant sources of copper. Arc Minerals’ share price went up in response and, in June this year, the company announced that its exploration programme is now fully funded, and drilling at both the Zamsort and Zaco projects will continue.
Could these projects eventually become Zambia’s newest copper mines?
***
Drilling is an essential part of every mining operation: during the early blasting process, and further down the line, too, such as when entry and exit points for workers are drilled within underground operations. But, without the drilling for core samples that happens during the mineral exploration stage, there would be no large-scale mining operations to speak of. Likewise, the more exploration projects that are funded in Zambia, the more that mining operations can grow, and the bigger the role that drilling will have.
Source: Mining for Zambia