Sandvik’s battery electric TH665B to lead its packed line-up for IMARC
Australian miners will have their first opportunity to view the world’s largest battery electric truck for underground mining in person when Sandvik’s TH665B makes its Australian debut at the International Mining and Resources Conference (IMARC) in Sydney in November.
With BEVs essential to helping mining companies reduce emissions, a TH665B will take centre-stage at the Sandvik stand before it heads to Western Australia for a trial with Barminco and AngloGold Ashanti at Australia’s Sunrise Dam gold mine. The 65 t truck’s lithium-iron phosphate battery and electric driveline deliver a remarkable 640 kW of continuous power, with zero emissions underground.
“There’s an enormous excitement around the Sandvik TH665B, and we’re delighted to be able to present it to visitors at IMARC,” says Wayne Scrivens, Vice President, Sales Area Australia & New Zealand, Sandvik Mining and Rock Solutions. “With the vehicle due to formally come onto the market in 2023, this is an excellent opportunity for customers to better understand just what it’s capable of.”
He adds: “Australian miners are increasingly introducing zero-emission underground mining equipment to reduce the carbon footprint of their operations. The Sandvik TH665B will complement products, such as our LH518B BEV loaders already on the ground in Australia, to help create safer underground environments with less heat and fewer diesel emissions.”
The truck forms part of a packed line-up of advanced mining technologies to be showcased by Sandvik at IMARC, including new solutions for development drills and advanced simulation packages.
Same drill, multiple roles
Another highlight at the Sandvik stand will be the Sandvik DD422i with Dual Controls Package, which helps operators of Sandvik’s DD422i and DD422iE face drills to optimise fleet versatility and performance. The package was developed in cooperation with contract miner Byrnecut, using the same drilling platform for multi-task operations.
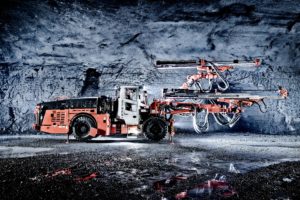
“Customers might currently be using conventional Sandvik DD421 hydraulic-controlled jumbos for ground-support work, and our intelligent Sandvik DD422i and Sandvik DD422iE drill rigs for boring, where they require long and accurate rounds with minimized overbreak,” says Wayne Scrivens. “With the Dual Controls Package, they can use a single drill for multiple and different applications.”
Being able to use a single drill for boring, bolting and meshing Sandvik says dramatically improves flexibility and has other benefits, such as increased commonalities in spare parts, service principles and general ease of use across the whole fleet. “It’s another example of how we’re working closely with customers to come up with the best solutions for the local industry,” says Scrivens.
Simulators to hit the ground running
Also on display will be Sandvik’s Digital Driller™ underground drilling simulator, which provides a safe and convenient way to train teams on the DD422i, DD422iE and DT922i drill rigs. Designed to improve operator and drilling performance, the fully mobile system weighs less than 50 kg.
“Using the simulator feels just like operating a real rig, as you’re using authentic controls and the same control system components that are installed on the drills themselves,” says Scrivens. “The trainer can initiate machine faults, incidents or hazards to train and assess operators. This teaches the user to respond correctly to any scenario, with maximum efficiency.”
Making use of the simulator means operators hit the ground running, which improves efficiency and productivity from the start. There is also no risk of equipment damage, zero consumption of rock tools and fuel, zero emissions and no exposure of the trainees to risk while familiarising them with a new drill rig.
Conference visitors will also have the chance to see the Sandvik AutoMine® Training Simulator. Available in two, light-weight trolley cases, it allows users to train on Sandvik’s automation system for loaders and trucks without tying up a machine or production, saving money without sacrificing production time. The Simulator uses the same controls and control system software as the AutoMine® system and is also an effective tool for advanced technical training for AutoMine® technicians.
Meanwhile, AutoMine® G Training uses Oculus headsets and controllers to create an effective and immersive way to learn in an interactive environment. Users can experience and interact with a 3D virtual reality environment to master the complete process of the AutoMine® system start-up procedure without the need for machine or production area allocations.
Attendees will also have another opportunity to virtually immerse themselves with the Sandvik Rock Processing Solutions’ virtual reality system. Users can walkthrough real-world plants that have been engineered, designed and built by the Sandvik Rock Processing team, exploring the various site and equipment options available.
An overview of your fleet
Another highlight of the Sandvik stand will be the demonstration of the My Sandvik customer portal. Recently redesigned, the portal allows customers to access a wide variety of information on their fleet, request quotations, and place orders at any time.
“The My Sandvik portal is highly intuitive and makes interacting with the company on a digital level simple,” says Scrivens. “The tasks you can carry out via the portal include shopping for more than 130,000 products and accessing online interactive manuals for technical, operational and maintenance manuals. You also have a complete overview of your fleet, including location, status, warranty dates and more.”
Meanwhile, attendees will have the opportunity to learn about Sandvik Ground Engaging Tools (GET), which provide the ultimate protection for your bucket, significantly extending life and reducing costly downtime. The Sandvik stand will also include a range of market-leading Rock Tools to improve productivity, profitability, sustainability and safety.
Following Sandvik’s acquisition of digital mining-technology company Newtrax, customers can learn how technologies such as collision avoidance systems are making mining safer. Visitors will also be able to learn about the potential benefits of Sandvik’s acquisition of DSI Underground, a global leader in ground support and reinforcement solutions for the underground mining and tunnelling industries.
Source; International mining
33 total views , 1 views today