The Uphill Task of Removing Cobalt from the Battery Industry
Followers of Elon Musk are used to big claims on Twitter. The social media habits of the Tesla and SpaceX billionaire have landed him in legal hot water on several occasions. But for the battery industry one boast stands out: a tweeted pledge to remove an obscure mineral mined in the Democratic Republic of Congo from the next generation of Tesla’s electric cars.
Batteries are the key component in the electric car revolution that Tesla kickstarted, and each one contains cobalt. Yet concerns about human rights abuses and child labour have prompted a dual effort to cut the amount of cobalt used in batteries and to clean up complex global supply chains.
The battery industry accounts for the majority of global cobalt demand, and that demand is set to soar with more than $60bn (£46bn) of investments in new battery factories during 2019, according to the data firm Benchmark Minerals. Musk tweeted his pledge in 2018 but demand for cobalt has since accelerated. Benchmark’s forecasts suggest that global demand for cobalt in 2029 will be 300,000 tonnes compared with an estimated 70,000 tonnes used in 2019.
The car industry is by no means the only one implicated: the electronics manufacturers Apple, Google, Dell and Microsoft, as well as Tesla, were named in a US lawsuit last month by families who say their children were killed while mining cobalt used in their products. However, the surge in electric car sales – as regulations limit exhaust pipe carbon dioxide emissions – and the kilograms needed in each car mean that cobalt supply concerns will only become more acute.
There are as many as 150,000 artisanal miners in Kolwezi, the regional capital in southern DRC that has become a major mining centre, according to Mark Dummett, a researcher on business and human rights at Amnesty International. Children working at the mines are easy to find within a five-minute drive of the city centre, he said.
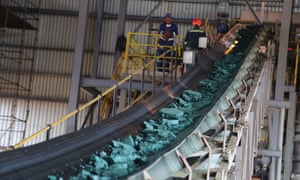
There has been some progress. The Congolese government has promised to pilot regulated areas for artisanal miners. Increasing consumer awareness has also led to supply chain auditing projects such as the Responsible Sourcing Network, run by the nonprofit organisation As You Sow, as well as two industry-led bodies, the Initiative for Responsible Mining Assurance and Responsible Mining Initiative, to ensure that suppliers are up to standards set by the Organisation of Economic Co-operation and Development.
Cobalt’s human and financial costs, as well as the technological imperative to increase energy density, have prompted research efforts by battery makers to reduce their reliance on the metal.
Most electric vehicle batteries use lithium ions, with nickel, manganese and cobalt (NMC) in various proportions in the cathode, a key part of any battery. Early batteries contained the three metals in equal proportions, but companies such as South Korea’s SK Innovation and LG Chem are close to producing cathodes with 80% nickel and only 10% cobalt, known as NMC 811. However, chemists have struggled to remove all cobalt, which is prized for stabilising the battery during recharging.
The FTSE 100 chemicals company Johnson Matthey has been working on reducing the amount of cobalt in its enhanced lithium nickel oxide (eLNO) batteries at one of its research labs in Sonning Common, near Reading. Its batteries, thought to contain higher levels of manganese, could cut cobalt costs in half, according to analysis by Bloomberg New Energy Finance.
Johnson Matthey chose Poland for a factory to mass-manufacture the products, opening in 2022, which will eventually produce 10,000 tonnes of battery material a year. BASF and Umicore, rivals from Germany and Belgium, are also working on lower-cobalt chemistries.
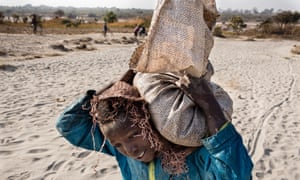
The demand for batteries has pulled in investors from unlikely places. The US miner Platinum Group Metals is funding research by Florida International University into using palladium and platinum in battery cathodes and electrolytes, potentially delivering improvements to recharge speeds and stability.
The company’s chief executive, R Michael Jones, hopes that these technologies – which are still years away from prototype stage – will sustain demand for palladium and platinum, which are used for catalytic converters in internal combustion engine cars.
Smaller British companies are also in the race, hoping to emulate the Nobel prize-winning Oxford University researchers who pioneered the lithium ion battery in the 1970s. Oxis Energy, based in the same research centre, is trying to develop lithium sulphur batteries with a claimed five times the energy density of current technology.
Yet Caspar Rawles, a senior analyst at Benchmark Minerals, cautions that it will be years before battery manufacturers manage to eliminate cobalt completely. Recent price volatility has limited investment in new capacity, and the two-year shutdown of Glencore’s Mutanda mine near Kolwezi could mean that artisanal miners become a key source of the metal as demand increases.
Tesla’s first Model S, launched in 2012, was built with an average of 11kg of cobalt per vehicle, but according to Benchmark Minerals that was down to about 4.5kg in its successor car, the Model 3, which launched in 2018. That has been achieved using a nickel-cobalt-aluminium chemistry. However, further reductions in line with Musk’s ambitions could be significantly harder. Tesla declined to share more details of its cobalt-reduction plans with the Guardian.
Either way, battery makers have a responsibility to the people of DRC, many thousands of whom rely on cobalt mining for a living, said Amnesty’s Dummett. “It’s still a relatively new sector, and now is the opportunity to adopt responsible sourcing,” he said.
Source: The Gardian